With more and more infrastructure projects, the market demand for aggregates in various countries is increasing day by day, and the process design of the crushing production line has become the primary concern of investors. This article introduces the process design of sand and gravel crushing plant from the aspects of host equipment selection, workshop layout, and environmental protection.
Main equipment selection
The sand aggregate production line can be simply summarized as crushing, screening, and storage. In order to obtain aggregate products with all indicators in line with the standard, the selection of host equipment will become the primary consideration in the design of the production line.
1. Selection of feeding and screening equipment
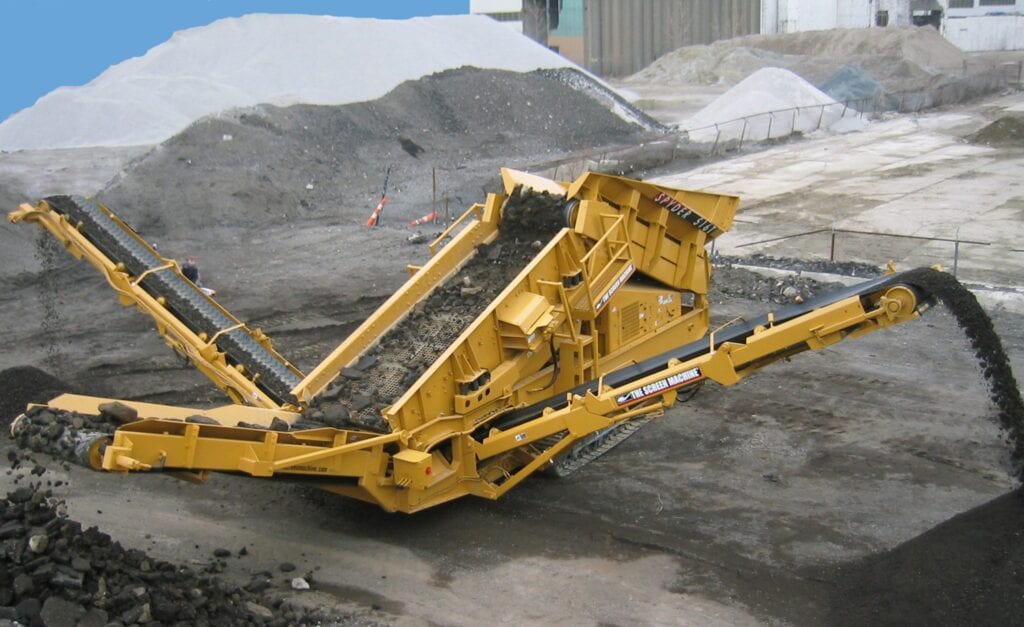
Aggregate products have relatively high requirements for soil content. In the design, a feeding device that can remove soil from the source is generally configured before the material enters the coarse crushing. Therefore, the vibrating screen feeder is the better choice.
When the raw material contains less soil and the material is relatively dry, the size between the screen bars of the vibrating screen feeder can be adjusted to an appropriate value, and the soil can be screened out after the material passes through the feeder.
When the raw material contains a lot of soil or the raw material is more viscous, you need to consider slightly larger the size of the feeder screen. Most of the soil (lump) waste is screened and then passed through a machine for sieving soil. The circular vibrating sieve will sift it clean. The stone material that has been sieved by the circular vibrating screen can be re-entered into the secondary crushing equipment for crushing.
2. Selection of crushing equipment
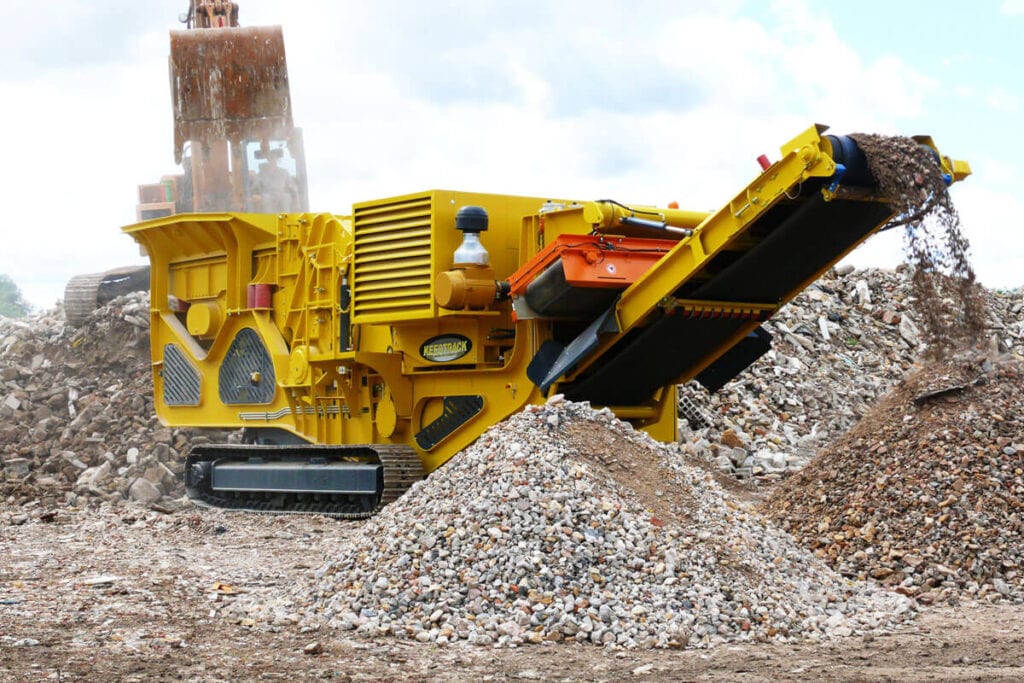
Crushing equipment can be divided into two categories: compression crushers and impact crushers.
Generally, compression crushers (such as gyratory crushers, jaw crushers, cone crushers) are suitable for harder rocks (such as granite, basalt, etc.).
Impact crushers (such as impact crushers, vertical shaft crushers, hammer crushers) are suitable for rocks with low hardness and low abrasiveness (such as limestone, etc.).
The following introduces two typical aggregate crushing equipment configurations
First, for hard rock, which has high hardness and abrasiveness index, choose jaw crusher, cone crusher and vertical shaft impact crusher combination, choose vertical shaft impact crusher, because the cone crusher crushes The aggregate pin flake content of the aggregate is too large, which does not meet the standard.
Second, for limestone with moderate hardness and abrasiveness index, select jaw crusher and impact crusher combination or reaction crusher and impact crusher combination.
For the equipment information of these two aggregate solutions, there is a more detailed introduction at crusherandparts.com.
Note: Generally, hammer crushers are rarely used in the production of aggregates. Although the hammer crusher is a one-stage crushing process, the process is simple, but after the hammer is broken, the yield of the large aggregate is low, it is easy to be crushed, and there are many powder materials. The finished aggregate will produce micro-cracks and reduce the compressive strength, which affects the aggregate quality and sale.
3. Selection of finished screening equipment
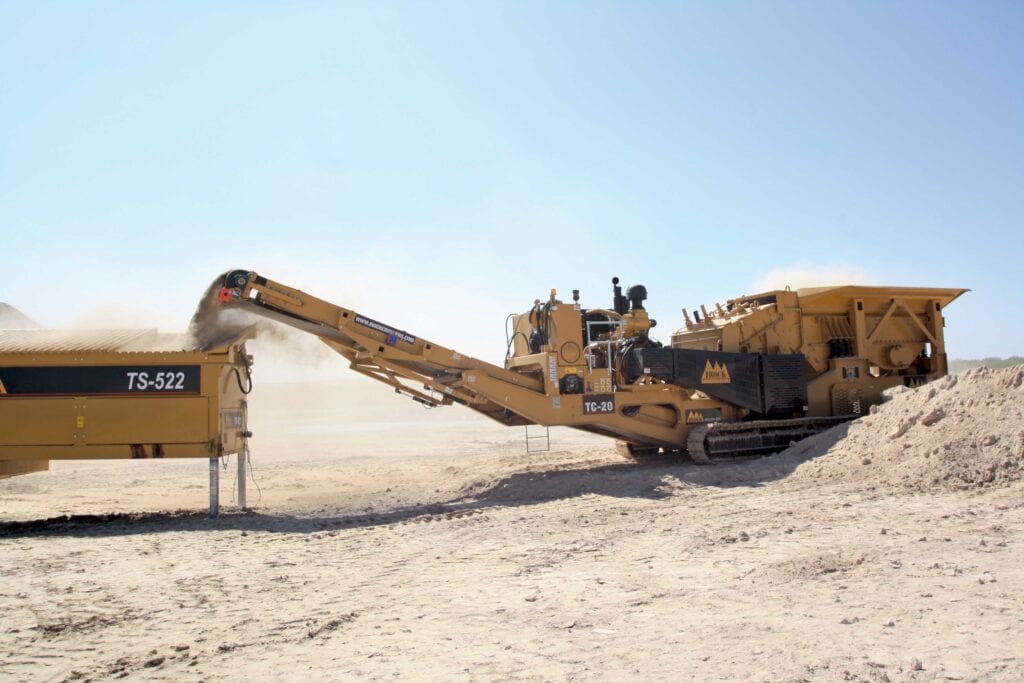
Generally, the circular vibrating screen is used for screening equipment in the aggregate industry.
Precautions for workshop layout
1. Selection of the effective volume of the front hopper of the crusher
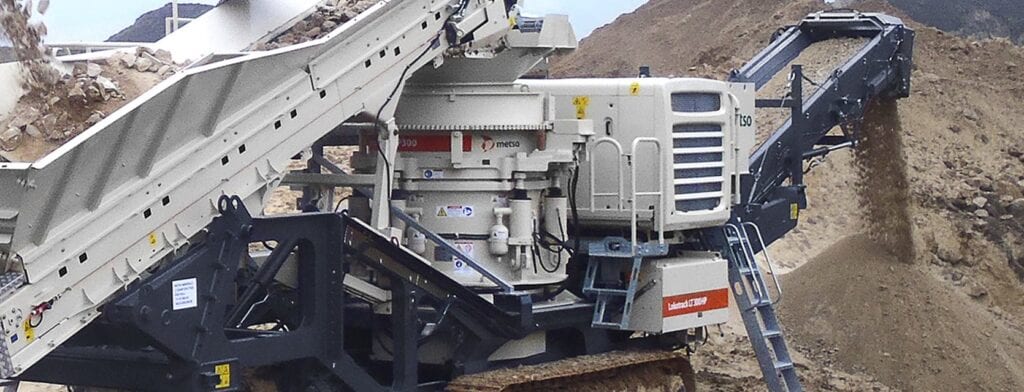
In general, the effective volume of the hopper design should meet the following two conditions at the same time
- No less than the workload of continuous operation of the crusher for 12-15 minutes.
- The carrying capacity of no less than 3 transport vehicles.
2. The layout of the crushing workshop
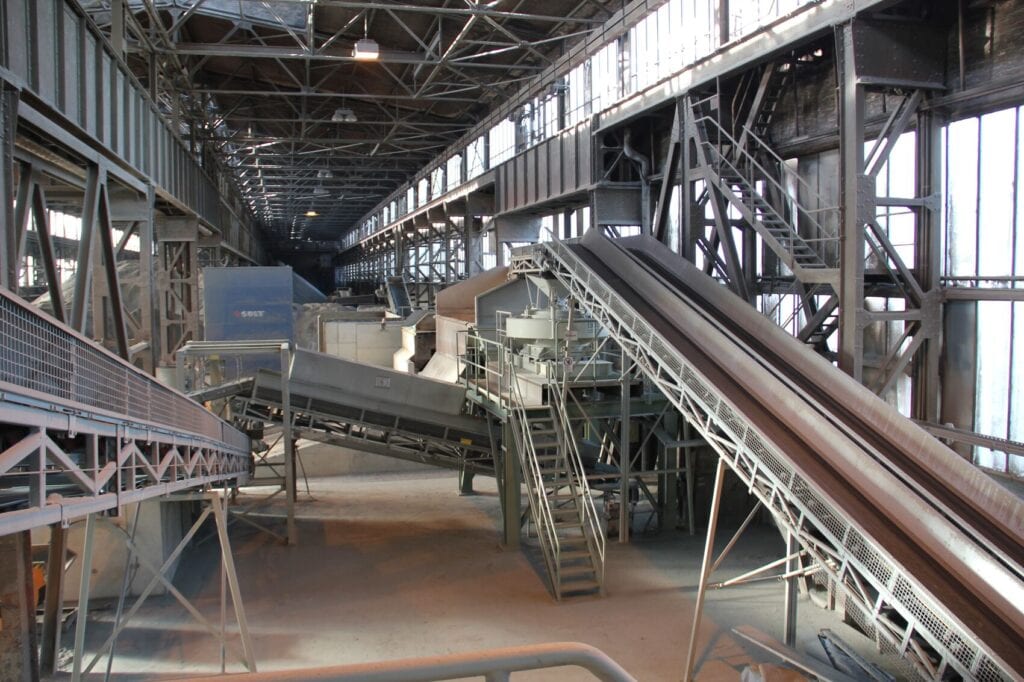
The layout of the crushing workshop should not only take into account the smooth flow of materials in and out of the crushing process, but also make full use of the terrain and altitude differences, and try to arrange the crushing plant on the same horizontal plane. In this way, not only the investment in civil construction can be reduced, but also the maintenance, inspection, and replacement of parts of the crusher are convenient.
3. The layout of the screening workshop
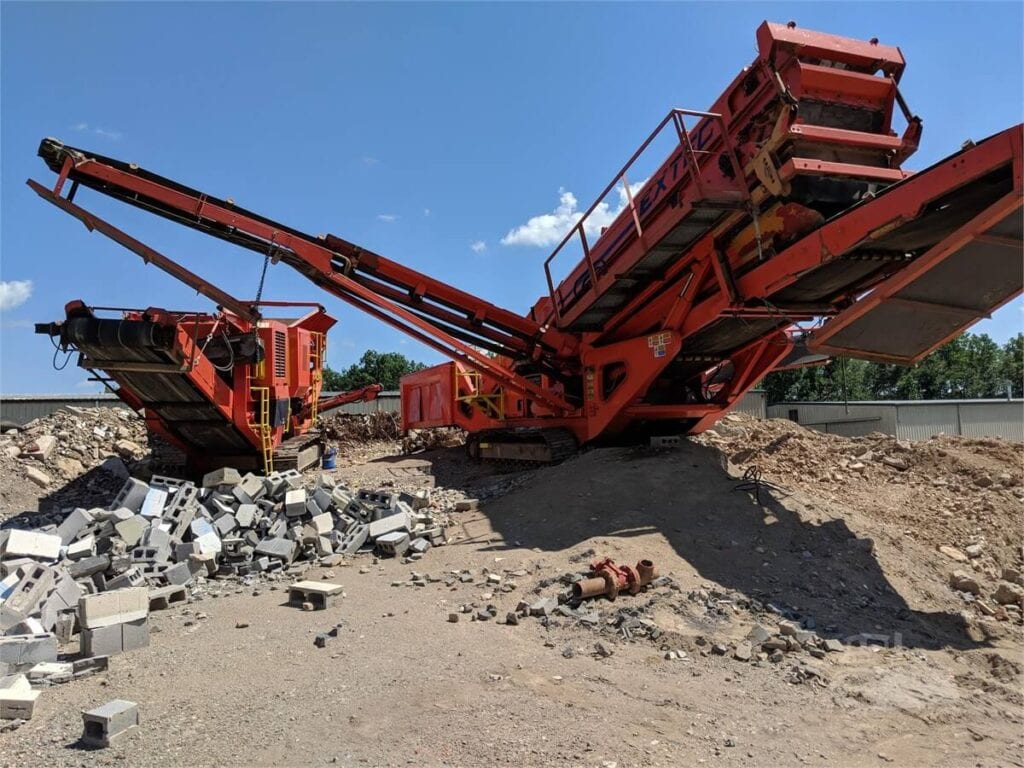
- The layout of the vibrating screen should be designed with an inspection platform around the equipment.
- The workshop should be closed, and the vibrating screen equipment itself should be sealed to avoid a large amount of dust overflow during screening.
- Convenient for dust collection treatment of dusty gas.
4. Finished product yard layout
In response to the national environmental protection policy, the storage of finished aggregates can be in sheds or warehouses. When storing the shed, in order to reduce the secondary dust from forklift loading, if the terrain height difference is available during the layout, try to design a loading belt conveyor under the stack.
Environmental protection matters
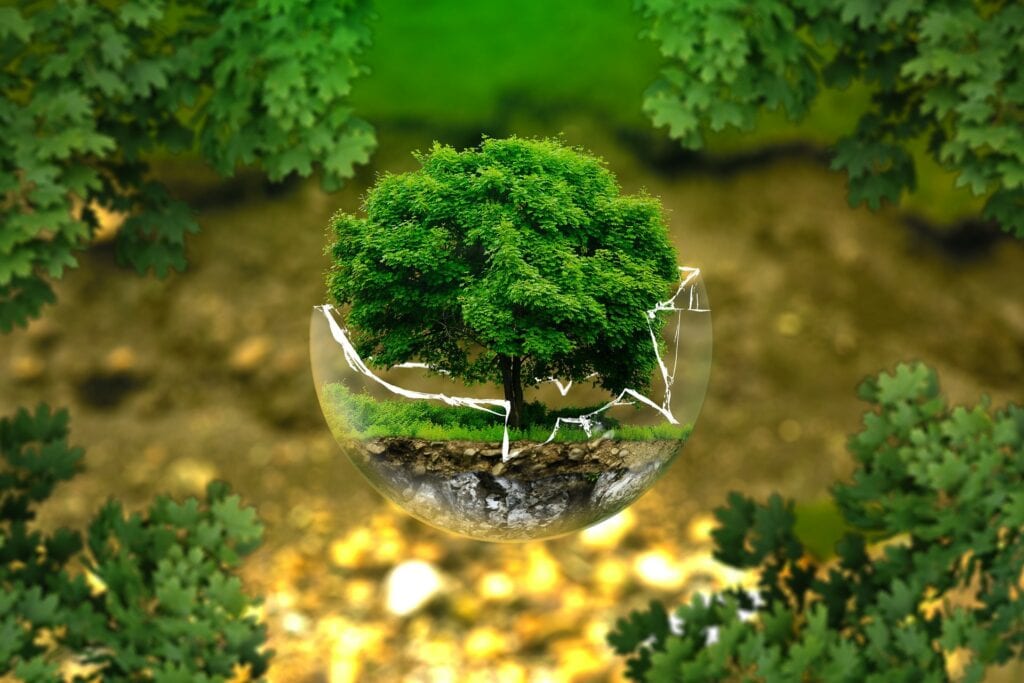
1. Sources of environmental pollution
The environmental pollution caused by sand and gravel production lines is mainly dust, noise, and sewage generated during the production process.
Dust mainly comes from the discharge points of crushing and screening equipment, transportation, and transfer points, finished aggregate storage and unloading points, and dust during outbound aggregate loading.
The noise mainly comes from the operation of crushers, vibrating screens, and other equipment.
The sewage is mainly domestic sewage and does not contain harmful substances.
2. Environmental protection measures
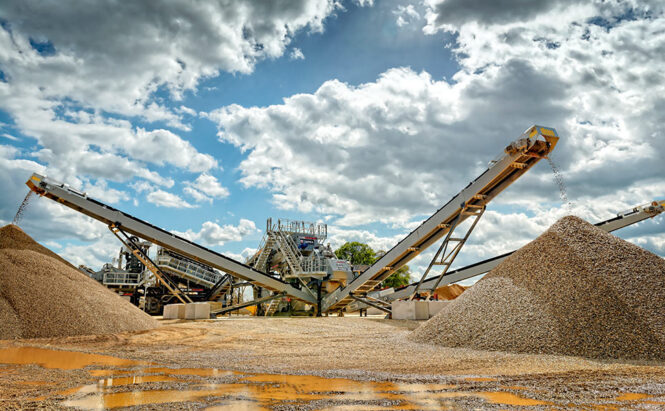
- Dust control measures
- Dust is generated in the whole process of aggregate production. In order to effectively control the amount of dust emission, the design is designed to minimize dust in the process, choose equipment with less dust, and use conveying and feeding equipment with good sealing performance. Pay attention to the shape and angle of the material pipe when designing the material pipe connected to the equipment to minimize the drop.
- All dust discharge points adopt high-efficiency dust collectors with high dust collection efficiency and reliable technology. Ensure that the dust emission concentration is less than 30mg/N㎡ and meet the emission standards.
- For the dust removal of the finished aggregate storage and unloading point, water spray dust removal can be selected according to the on-site water source. In factories in areas with tight water sources or cold areas in northern my country, storage and storage sheds can also be constructed to reduce dust emissions.
- Noise control
Noise control, first, choose low-noise equipment as far as possible from the equipment selection; second, arrange the noisy equipment in a closed workshop.
- Sewage treatment
After the domestic sewage is pretreated in the septic tank, it is used as water for greening, farmland irrigation, etc., and is not discharged; the water used for spray dust removal is consumption water, and it evaporates naturally after dust removal.
In view of the high content of clay in the raw materials of some mines in southern my country, in addition to the principle of selection of the host equipment introduced above, sometimes the finished aggregate still contains some clay lumps. If necessary, consider washing the aggregate.
The above are some suggestions in this article for equipment selection, workshop layout, and environmental protection measures in the design of sand and gravel aggregate production line. I hope it will be helpful to everyone!